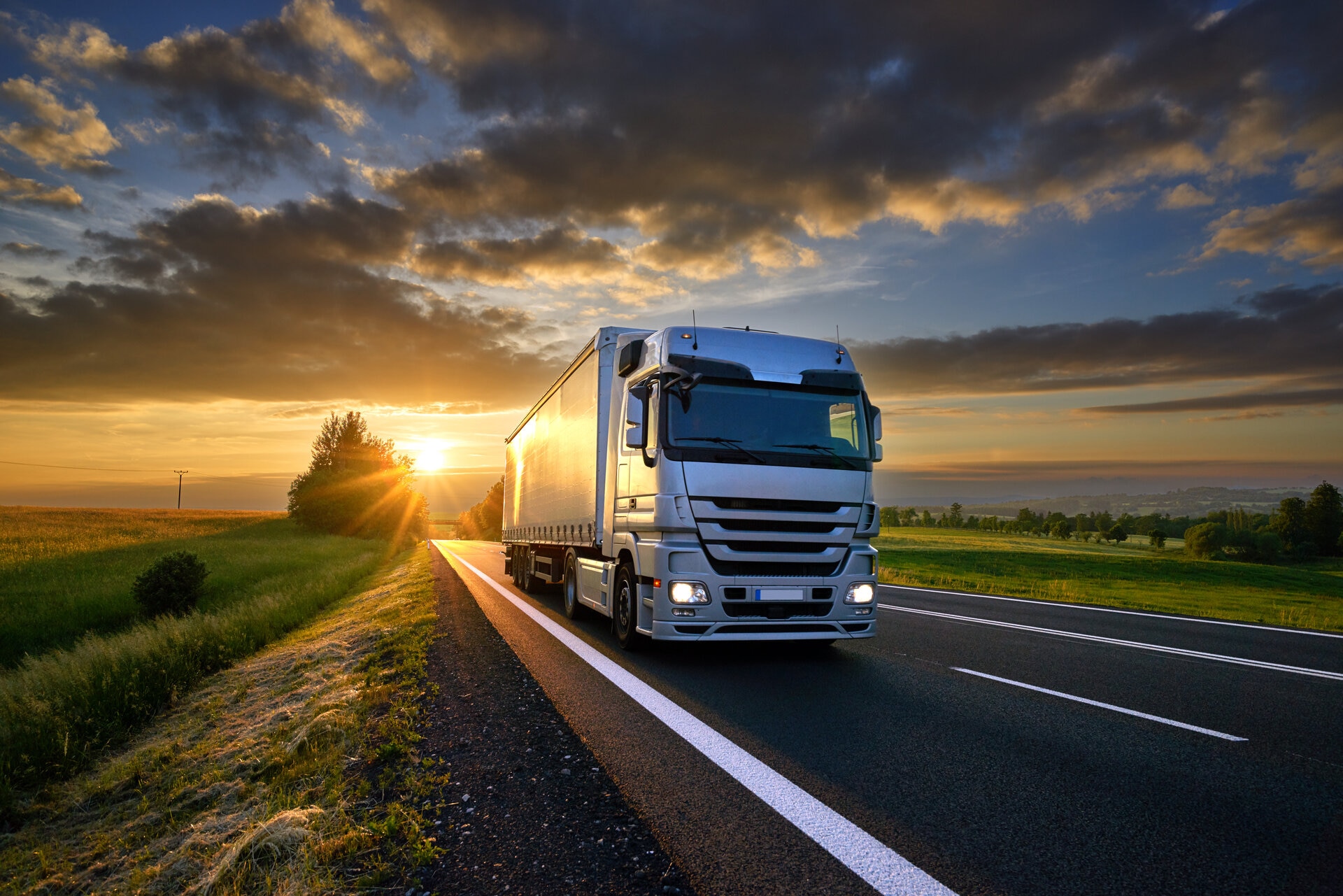
Insights
A collection of interactive tools and industrial insights
curated by the BatteReverse team
Stakeholder Map
The reverse logistics of batteries involves a diverse network of stakeholders, including industrial associations, research groups, NGOs, professional federations, and many others. Explore our stakeholder map to discover the dynamic landscape of the reverse logistics value chain and gain insights into the various actors operating within it.
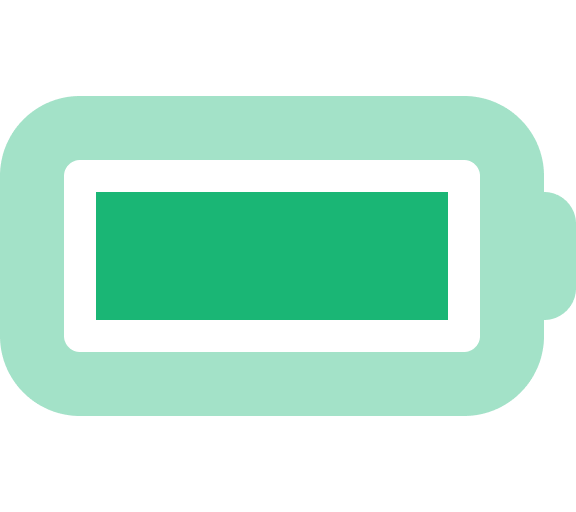
These companies produce battery cells according to the requirements of their application (e.g. electric vehicles). Each cells is made of cathodes, anodes, separator and electrolyte and they can have various shapes: cylindrical, pouch and prismatic.
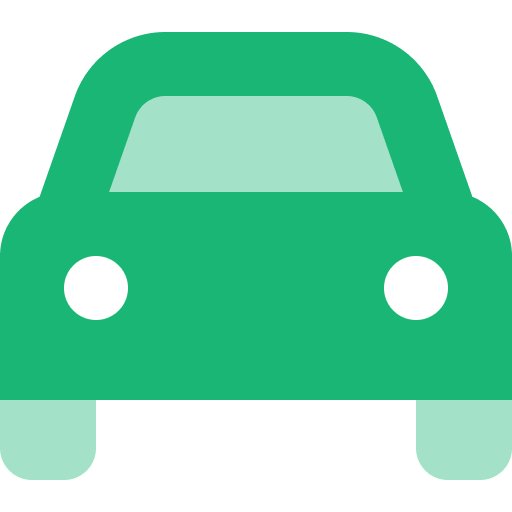
EV OEMs play a crucial role in the reverse logistics of batteries since they introduce EVs to the market and thus hold the Extended Producer Responsibility which means they are responsible for the treatment of batteries coming from the production process and from end-of-life EVs. EV OEMs also train their authorised workshops how to repair and extract batteries from EVs.
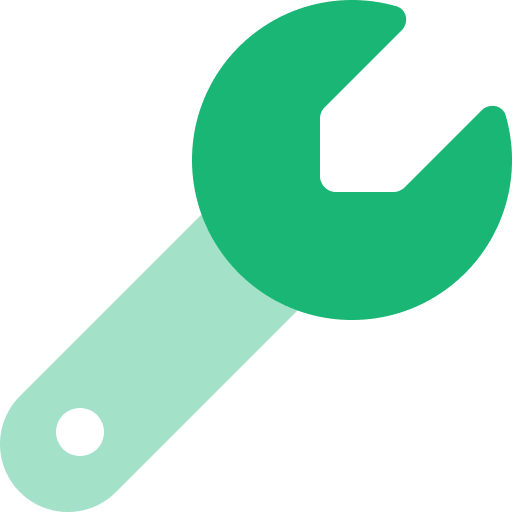
Refurbishers are typically independent car workshops specialised in repairs of electric vehicles. They perform assessment of batteries and replace damaged/degraded batteries to restore their original condition or upgrade it.
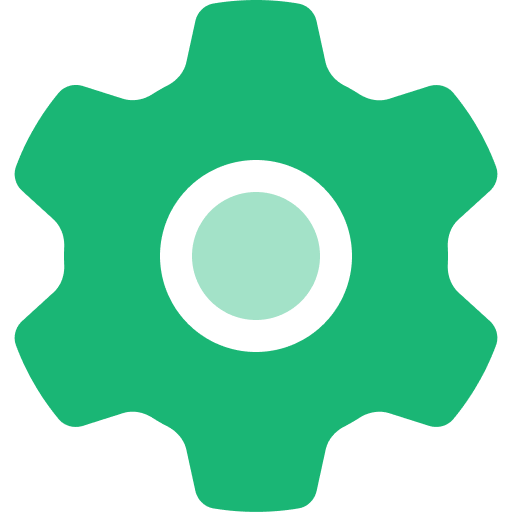
Car dismantlers (Authorised Treatment Facilities) are car recycling companies which hold a permit to dismantle and depollute scrap cars according to the End of Life Vehicle Directive. ATFs are the only organisations which can issue car owners with a Certificate of Destruction - a document to prove responsibility for the vehicle has ceased. Car dismantlers become the owners of parts from vehicles.
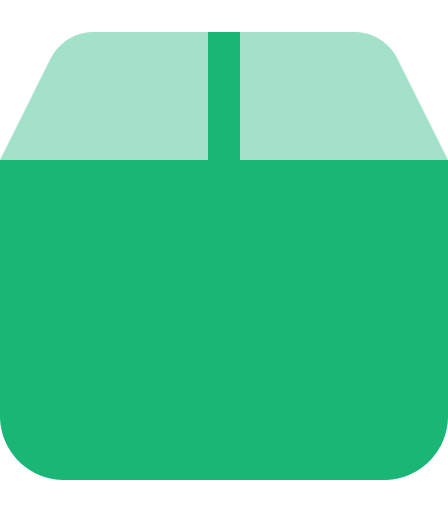
These companies produce packaging for safe transportation and storage of batteries which are used by logistic operators. There are several types of packaging which depend on the state of safety (SoS) of the battery which is defined by the battery owner (EV OEM, car dealership, dismantler): green (new and undamaged), yellow (prototypes, used and non-critically damaged) and red (critically damaged).
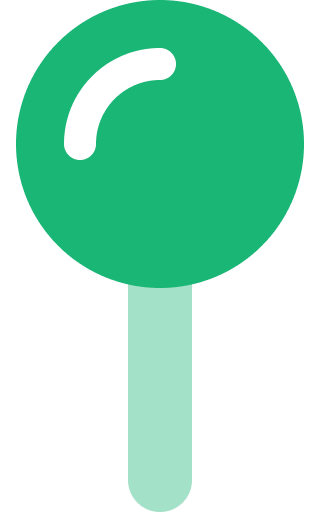
Battery collectors (or National Collection Schemes for Batteries) usually offer a wide range of services for EV battery disposal, e.g. they organise the collection of li-ion batteries from dealers and dismantlers as well as transport to the recycler or re-user in accordance with the preferences of the car producer. They also fulfil the reporting obligations.
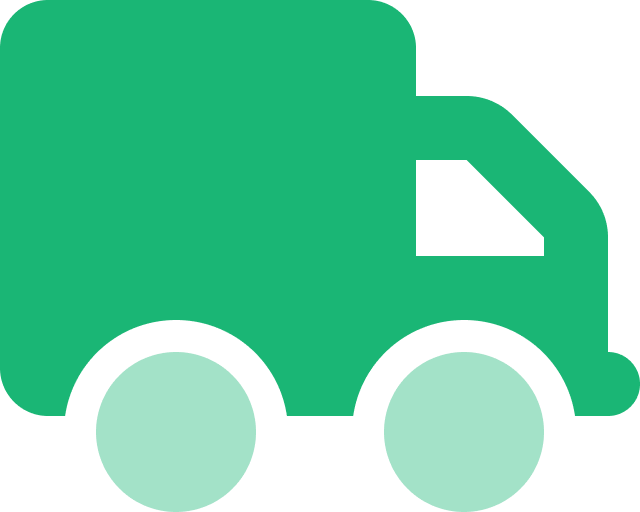
3PL operators are responsible for transportation of the battery packs and modules, ensuring compliance with environmental regulations and safety standards. These companies may work with recyclers or other companies that specialise in the processing of end-of-life batteries. 3LP for black mass is responsible for safely and securely transporting the black mass from the pretreatment plant to the metal refineries.
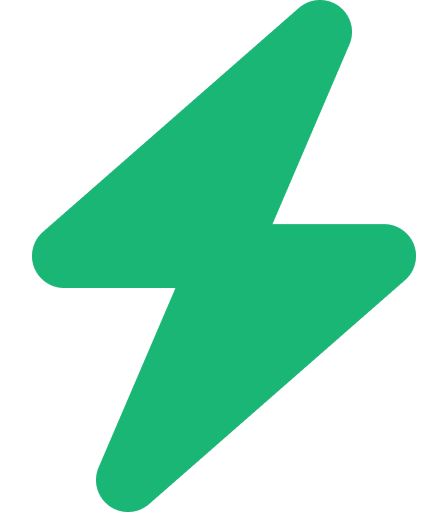
Repurposers give a new life to batteries that are no longer suitable for electric vehicles but have a sufficient state of health for less demanding applications. This stakeholder may use the whole battery pack or dismantle it into modules or cells to develop a new product. The two main applications for repurposed EV batteries are behind-the-meter (e.g. residential) and front-of-the-meter (grid scale) stationary energy storage systems.
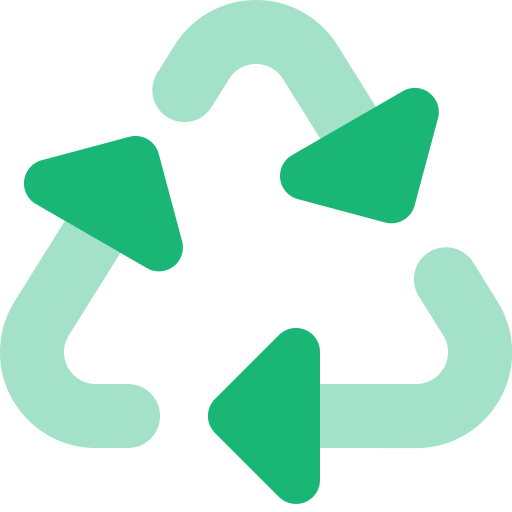
The pretreatment process involves discharge, dismantling, mechanical shredding and sorting. The outcome of this steps is a black mass which is a mix of the battery active materials (such as cobalt, nickel, manganese and lithium).These companies receive end-of-life batteries from different stakeholders (e.g. EV OEMs) and they send the black mass to metal rafineries.
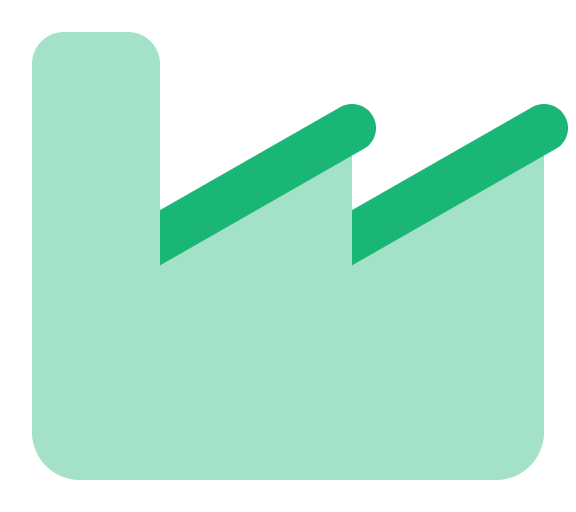
The material refinement companies collect black mass that comes from the pretreatment plant and refines it to get secondary raw materials such as nickel sulphate, cobalt sulphate, manganese carbonate and lithium carbonate. Modern facilities most commonly use a highly efficient hydrometallurgical process which involves steps such as leaching, solid-liquid separation, purification and precipitation. Resulting materials are sold to producers or cathode active materials.
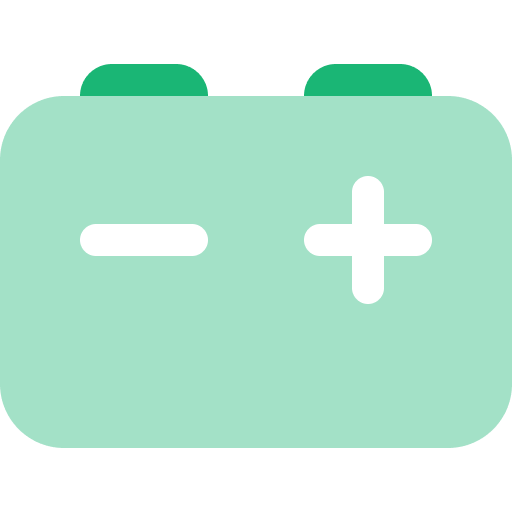
Companies thatuse a mix of software platforms and consultancy services to facilitate the full end-of-life management of EV batteries, including collection, logistics, testing, document generation, transfer of ownership, and data analysis of batteries.
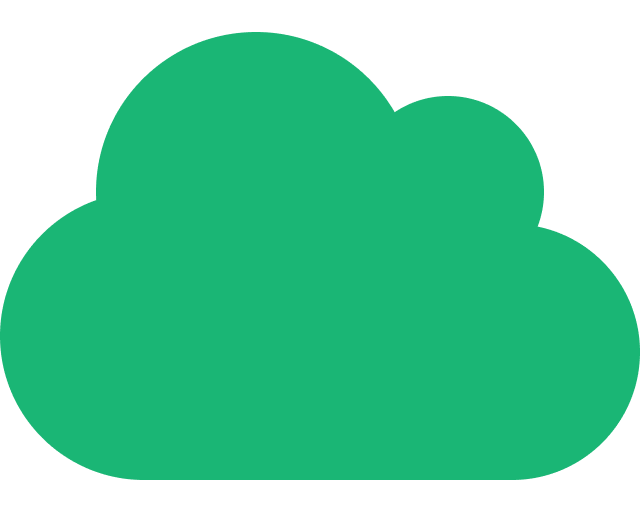
These platforms offer various data management services throughout the full life cycle of the battery, such as traceability, regulatory compliance, carbon footprint analysis, state-of-health characterisation and safety monitoring.

2nd life marketplaces help to connect supply and demand of batteries from EVs. Customers (individuals or businesses) can use these platforms to sell or buy batteries in the form of packs, modules or cells, while the marketplace operator usually handles the logistics, data exchange and transactions.
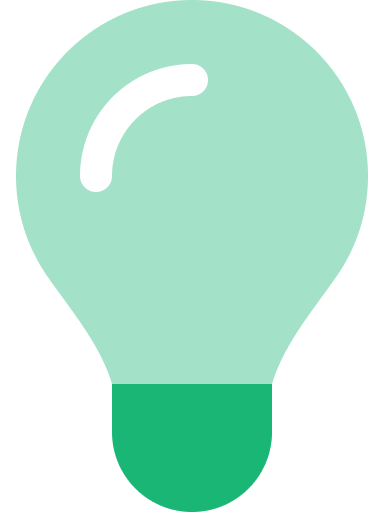
Research institutes and innovation actors help improve reverse logistics of batteries by advancing research on technologies and developing new business solutions. CEA, Inegi, Centria and UPV are the coordinators of Horizon Europe projects under the call HORIZON-CL5-2022-D2-01-10 which aims to develop streamlined collection and reversed logistics, fully automated, safe and cost-efficient sorting, dismantling and second use before recycling.
Circular Business Cases
Both established companies and startups are developing various business models to capture the full value of Li-ion batteries while improving their circularity. We’re showcasing how these models (e.g. remanufacturing, repurposing, recycling) have been employed either on commercial or pilot scale, providing details on stakeholders involved, economic and technical feasibility, identified barriers, and most relevant features/parameters that need to be optimised.

Bringing traceability to battery supply chains: digital product passports at Circularise
April 29, 2025
Discover how Circularise’s blockchain-based digital product passport supports EV battery traceability, regulatory compliance, and circular value chains - while safeguarding supplier IP.
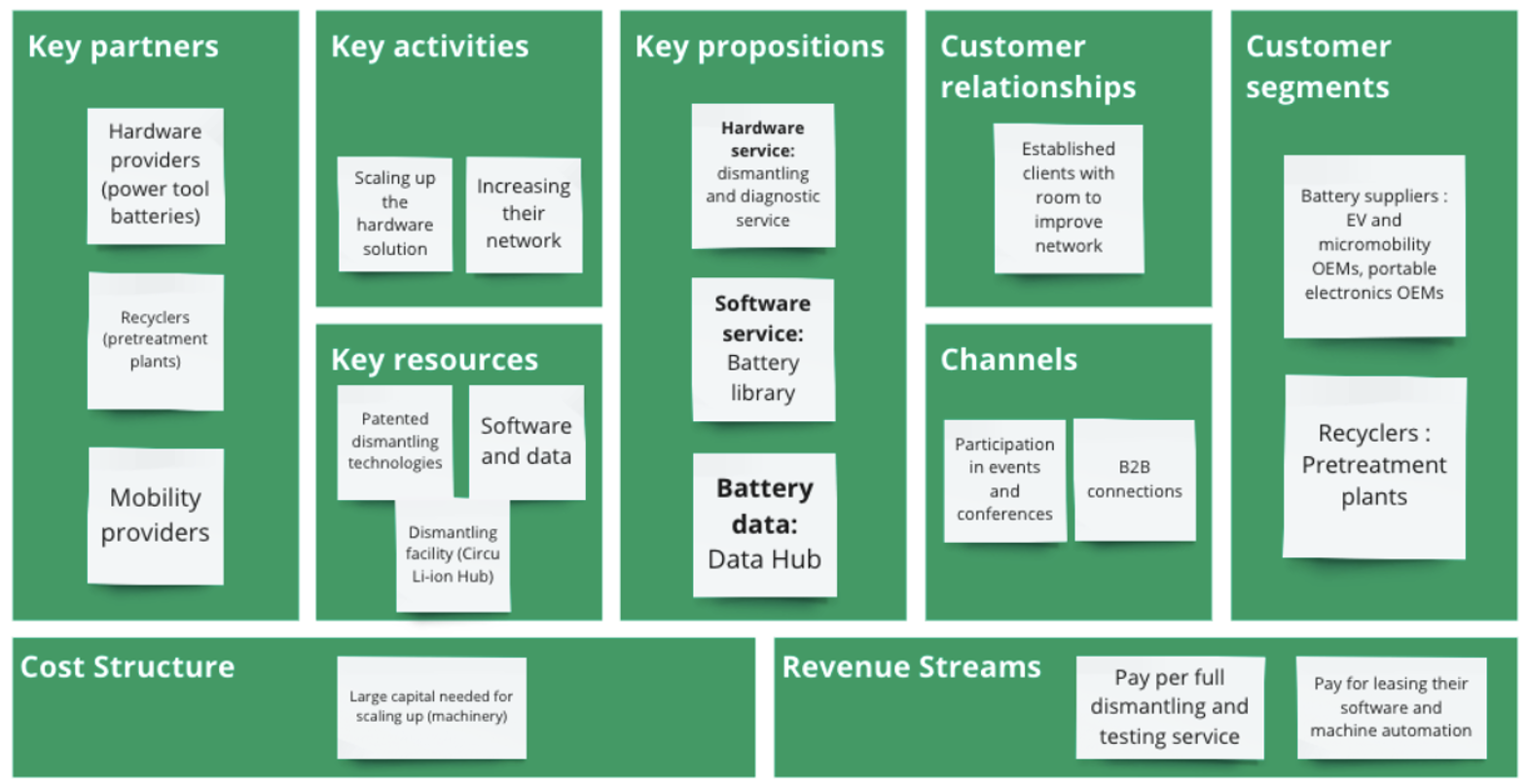
Automating reverse logistics of Li-ion batteries: disassembly at Circu Li-ion
January 13, 2025
Explore how Circu Li-ion is transforming reverse logistics through the automated disassembly of end-of-life lithium-ion batteries, reducing costs and emissions.
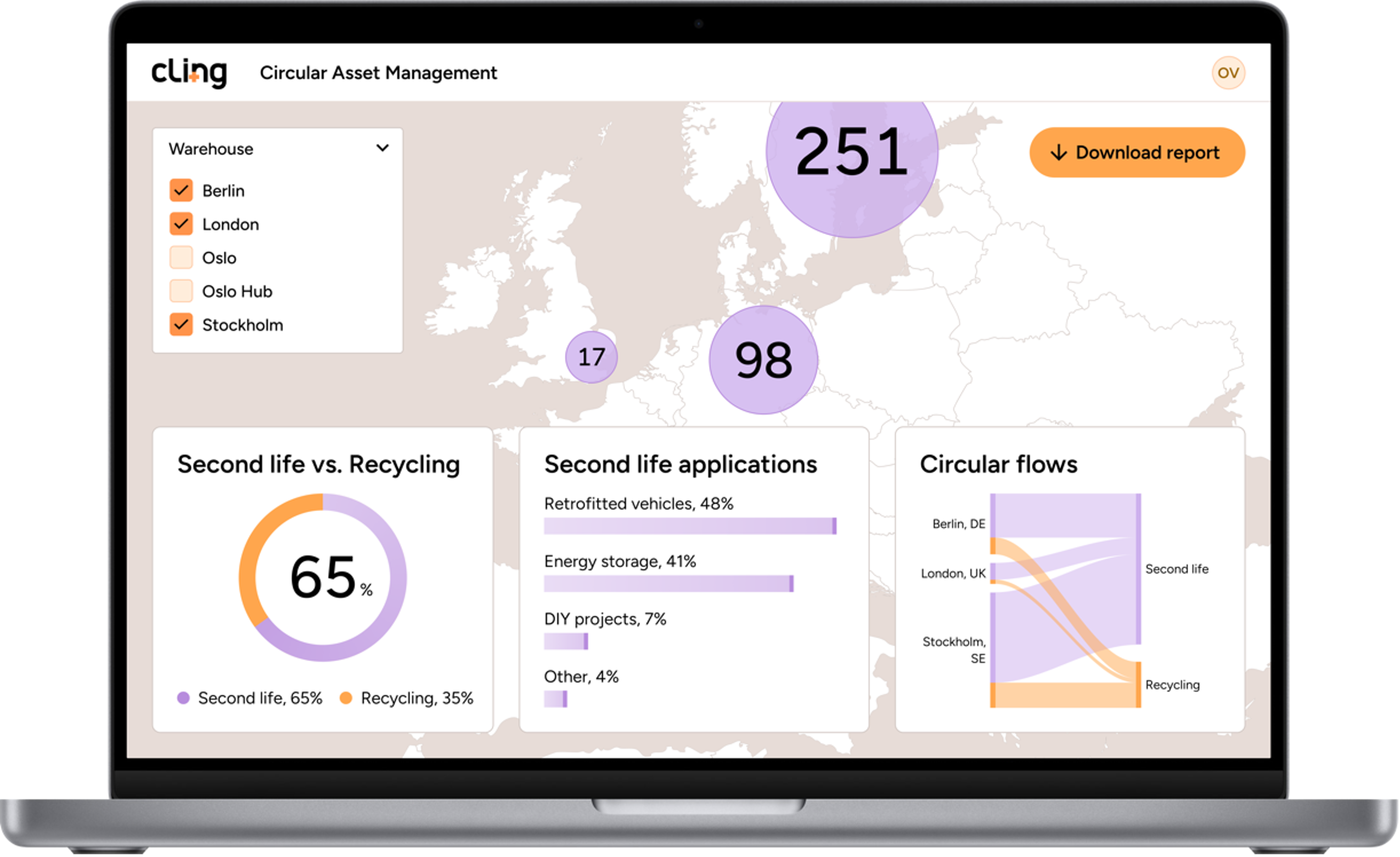
Enabling scalable trade: How Cling Systems’ platform aims for frictionless battery circularity
March 13, 2024
Cling Systems Market Lead, Eden Yates, and Head of Product Design, Valentin Loschinin, explain how they enable battery circularity by bringing together supply and demand for 2nd life batteries.
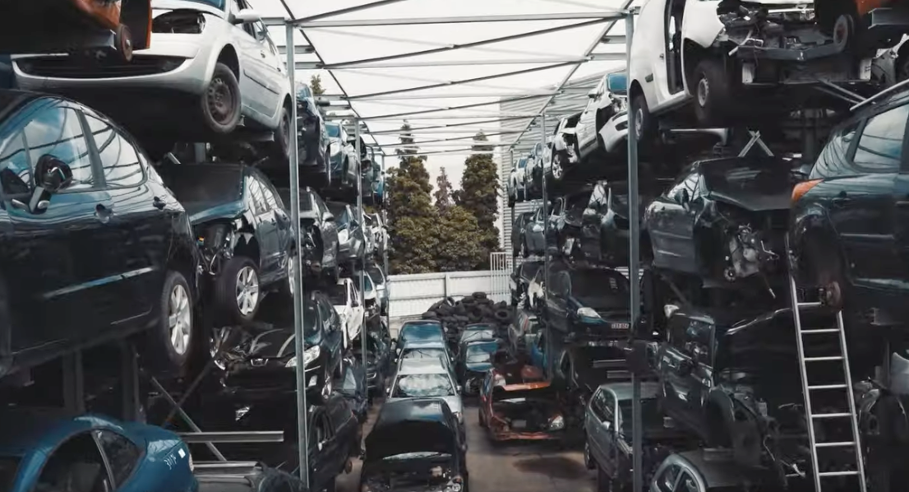
Helping producers become more circular: end-of-life EV management by Febelauto
March 4, 2024
Sophie Poidevin, the HEV batteries project coordinator at Febelauto, offers insights into the management of end-of-life electric vehicles (EVs) in Belgium and explores the pivotal role of producer responsibility organisations.

No battery should be wasted – sourcing batteries for 2nd life at Škoda Auto
December 12, 2023
Škoda Auto unveils the company's strategic approach to prolonging battery life, exploring second-life applications, and recycling.
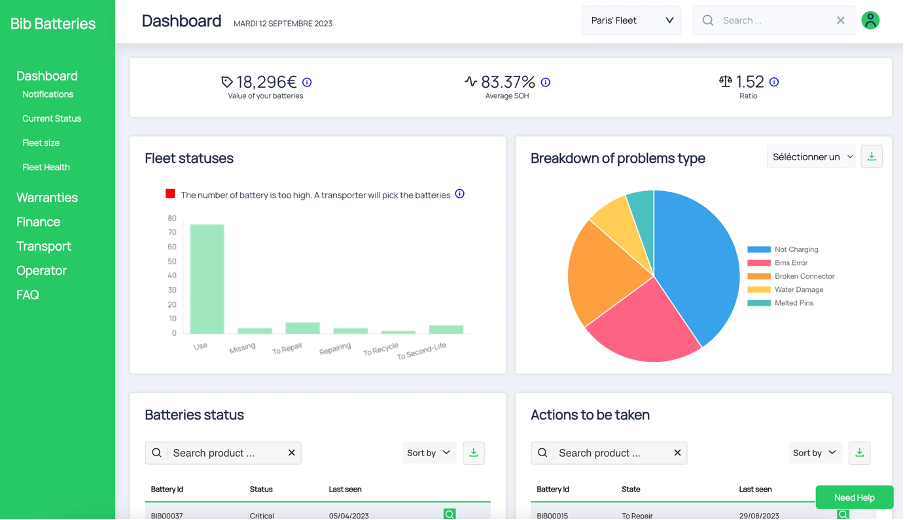
Maximising the lifetime of micromobility batteries: fleet monitoring by Bib Batteries
October 18, 2023
Robin Laffin, the Head of Operations at Bib Batteries, demonstrates how their data-driven solution helps to choose between repair, reuse, and recycle scenarios for retired micromobility batteries.
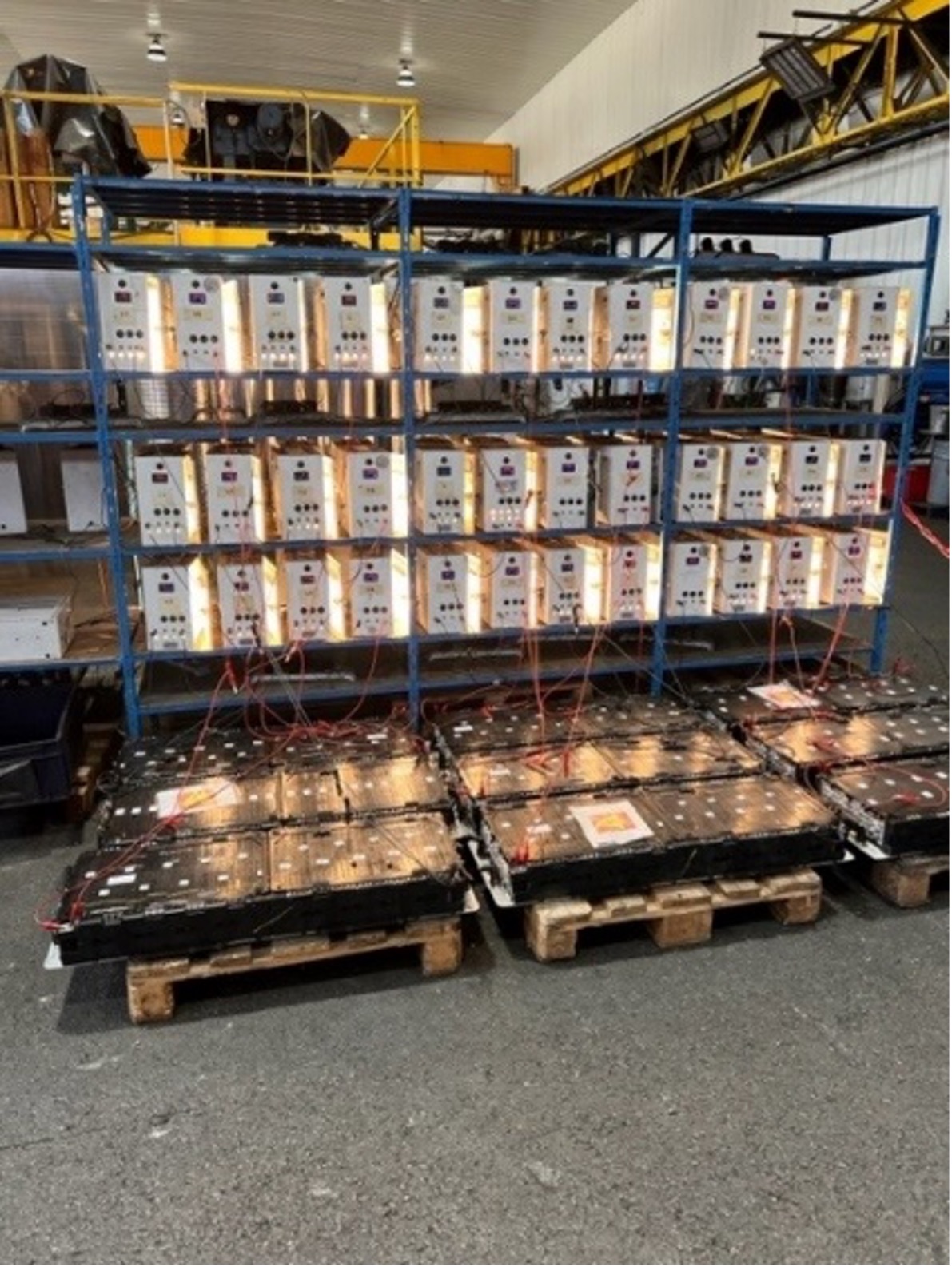
Transforming end-of-life battery packs into commodity-grade materials: recycling at TES
October 2, 2023
TES Innovation Director Dr. Farouk Tedjar talks about how their facility in Grenoble recycles EV batteries.
.jpg)
Giving a 2nd life to spent EV battery modules: repurposing at betteries AMPS
August 24, 2023
The Managing Director and Founder of betteries AMPS, Dr. Rainer Hönig, reveals curious intricacies and challenges of the battery repurposing business model.